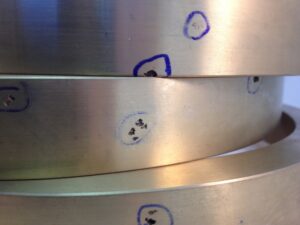
Repairing porosity in sand castings is a crucial process to ensure the structural integrity and reliability of the final product.
Porosity, characterized by voids or air pockets within the casting, can compromise the mechanical properties and functionality of the component.
The first step in addressing porosity is identifying and marking the areas exhibiting porosity. Clean these surfaces is crucial to remove any contaminants to ensure a clean and stable substrate.
Remove little by little material by mechanical grinding or flame gouging until there are no more visible holes. You want to remove as little as possible material so it does not become a major weld repair.
Weld build up layer by layer based on the chosen WPS and process, post weld heat treatment may be required relieves residual stresses induced by the repair process and ensures the casting undergoes a controlled heating and cooling cycle, minimizing the risk of thermal shock.
Post-repair inspection is a critical checkpoint to guarantee the effectiveness of the repair. Employing non-destructive testing methods, such as dye penetrant testing or radiographic examination, ensures that the repaired areas meet the required standards for quality and integrity.
Detailed records of welding procedures, heat treatment logs, and inspection reports need to be maintained for a designated period. This serves as a reference for future assessments but also contributes to traceability and quality assurance.
Quality control measures are embedded throughout the repair process to monitor and verify the effectiveness of each step. These measures, emphasize the importance of maintaining high standards in craftsmanship and precision to producing a repaired casting of the highest quality.
Cheers 🥂 MFR